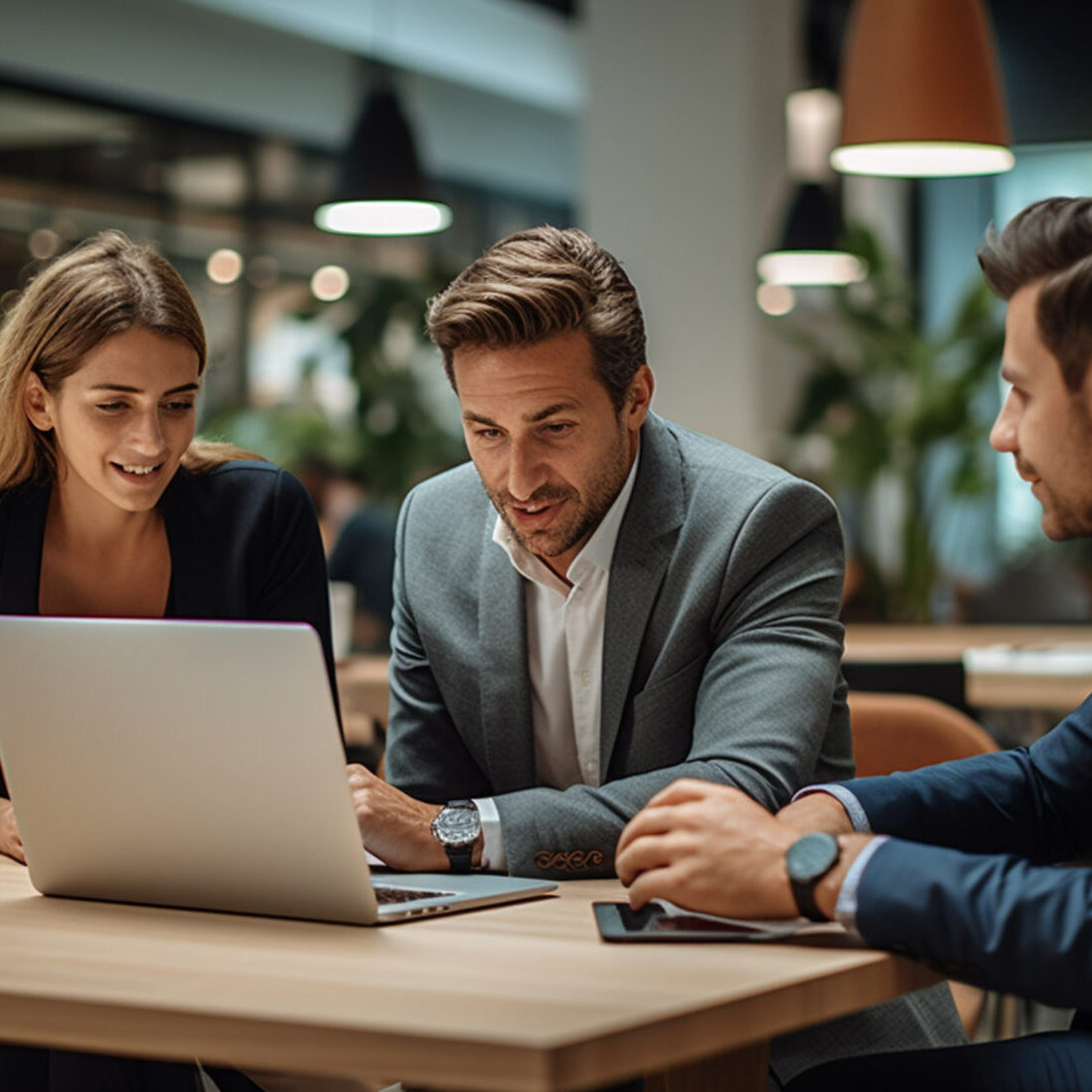
From Audit Non-Conformities to CAPA: A Systematic Approach
By Imane Nohair, GxP Audit manager at Apotech
An organized method from audit non-conformities to CAPA overview is key for operational efficiency and compliance in the pharmaceutical industry.
Continuous improvement, product quality, and long-term compliance can be assured when these non-conformities are successfully addressed through a Corrective and Preventive Action (CAPA) procedure.
This article describes an approach for using CAPA implementation to address audit non-conformities.
1. Identifying Non-Conformities
Non-conformities can arise from various sources, including:
- ๐ Internal audits: Routine quality checks identifying deviations from established standards.
- ๐ต๏ธ Regulatory inspections: External audits conducted by authorities such as the FDA or EMA.
- ๐ข Consumer complaints: Feedback from customers highlighting quality issues.
- ๐ญ Manufacturing process deviations: Variability in production processes leading to inconsistencies.
Early detection of these issues is crucial. Companies can leverage Electronic Quality Management Systems (eQMS) to centralise documentation, monitor non-conformities systematically, and track resolutions efficiently.
2. The Root Cause Analysis (RCA) Process
Instead of just managing the symptoms of non-conformities, addressing them demands a deep understanding of their root causes. Systematic failures can be found with the help of techniques like:
- ๐ Pareto Analysis: Prioritising issues based on frequency and impact.
- ๐ Ishikawa (Fishbone) Diagram: Categorising potential causes (human, materials, equipment, methods, etc.).
- โ The 5 Whys Method: Asking “why” multiple times (usually five) to find the real cause of a problem. Each answer leads to the next “why” until the true root cause is identified.
โ A comprehensive root cause analysis guarantees that the same problem does not reoccur because of an unidentified root cause.
Combining these techniques improves RCA effectiveness by prioritising key issues, exploring potential causes systematically, and getting to the root of the problem behind non-conformities.
3. Developing a CAPA Plan
Following the identification of the root cause, a SMART (Specific, Measurable, Achievable, Realistic, Time-bound) action plan must be developed to ensure effective remediation:
- ๐ Specific: Clearly define corrective actions.
- ๐ Measurable: Establish criteria to assess effectiveness.
- โ๏ธ Achievable: Ensure feasibility within resource constraints.
- ๐ Realistic: Align with operational capabilities.
- โฐ Time-bound: Set deadlines for implementation and review.
Key elements of the CAPA plan include:
- ๐ ๏ธ Corrective actions to immediately resolve identified issues.
- ๐ก๏ธ Preventive measures to mitigate recurrence.
- ๐ฅ Defined roles and responsibilities to enhance accountability.
4. Implementing the CAPA Plan
For CAPA implementation to be effective, organisations should:
- โ ๏ธ Prioritize corrective actions based on risk level.
- ๐ฌ Maintain open communication with relevant departments.
- ๐ Update Standard Operating Procedures (SOPs) to reflect necessary changes.
- ๐ Train employees on updated processes to prevent future non-conformities.
For example: If audits reveal documentation errors, preventive actions might include automating document reviews, while corrective measures could involve revising templates and conducting staff retraining.
5. Monitoring and Verifying CAPA Effectiveness
Following implementation, CAPA effectiveness must be evaluated through:
- ๐งพ Follow-up audits to confirm sustained compliance.
- ๐ Key Performance Indicators (KPIs): Examples include CAPA closure times, recurrence rates of non-conformities, and compliance audit results.
- ๐ Ongoing process monitoring and gathering employee feedback to detect potential gaps.
A comprehensive verification strategy ensures CAPA solutions remain effective over time without introducing new risks.
Conclusion: Turning Findings into Opportunities
A systematic CAPA methodology is necessary to transform audit non-conformities into opportunities for improvement.
By identifying root causes, implementing well-defined corrective and preventive actions, and regularly assessing their effectiveness, pharmaceutical firms can ensure:
- ๐ฌ Compliance
- ๐ Improved product quality
- โป๏ธ Continuous improvement
With the integration of technological advancements and structured process improvements, organizations can not only resolve existing non-conformities but also build a proactive quality management system that prevents future compliance risks.