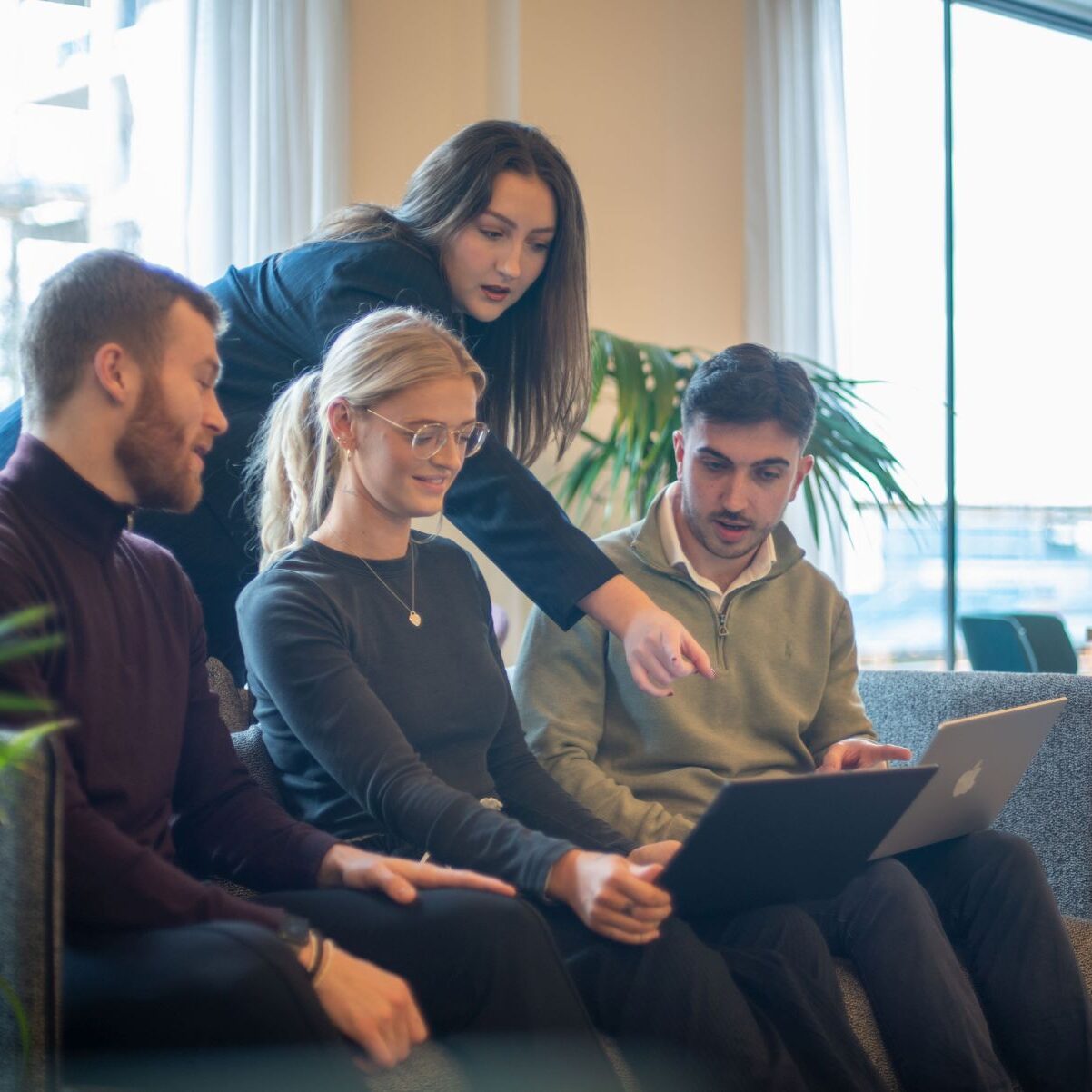
Quality Systems & Compliance
Quality Compliance for In Vitro Diagnostic (IVD) devices encompasses the organizational structure, procedures, processes, and resources implemented by manufacturers to ensure that their IVD products consistently meet regulatory requirements, specifications, and quality standards throughout the product lifecycle.
Compliance with IVD quality system requirements is essential for ensuring the safety, effectiveness, and reliability of IVD devices used in clinical practice. Apotech can support you to meet the rigorous standards of ISO 13485:2016, U.S. FDA CFR 21 part 820, and the Medical Device Single Audit Program (MDSAP).
Trusted by top-tier teams worldwide
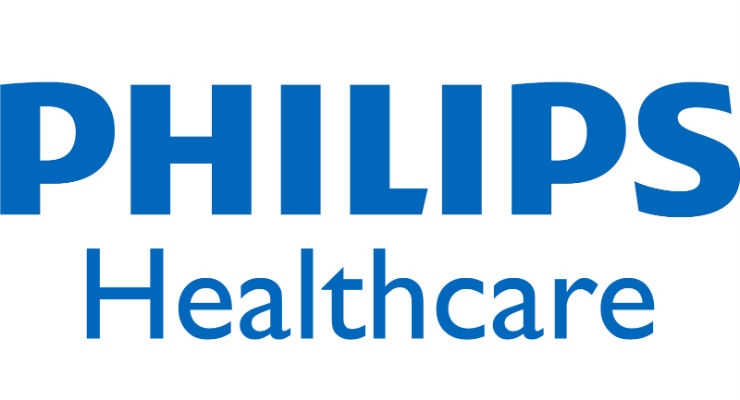
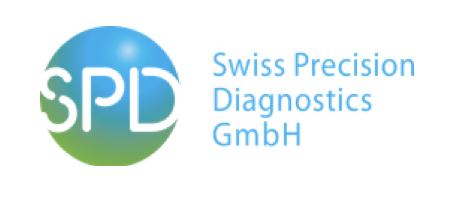
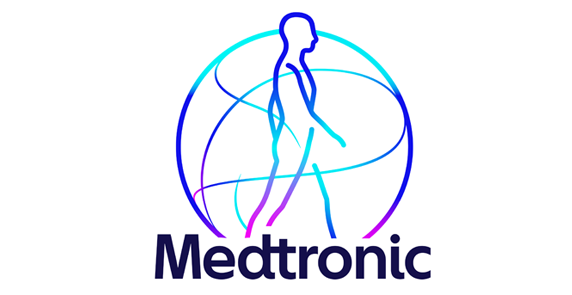
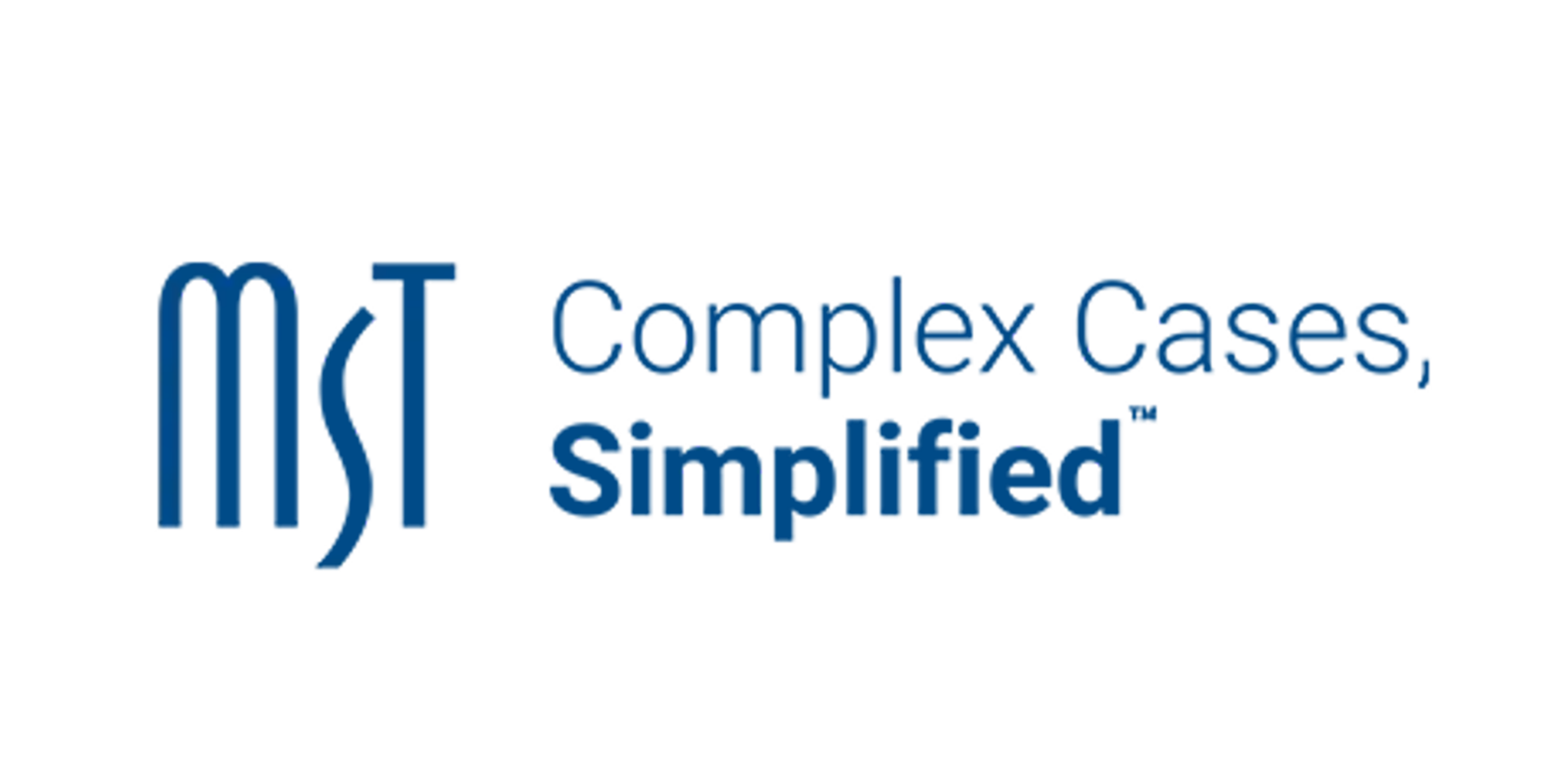
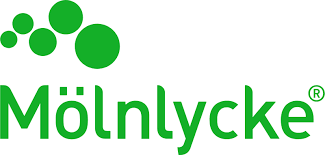
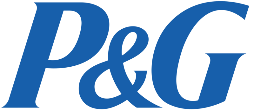
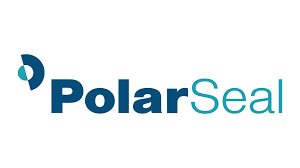
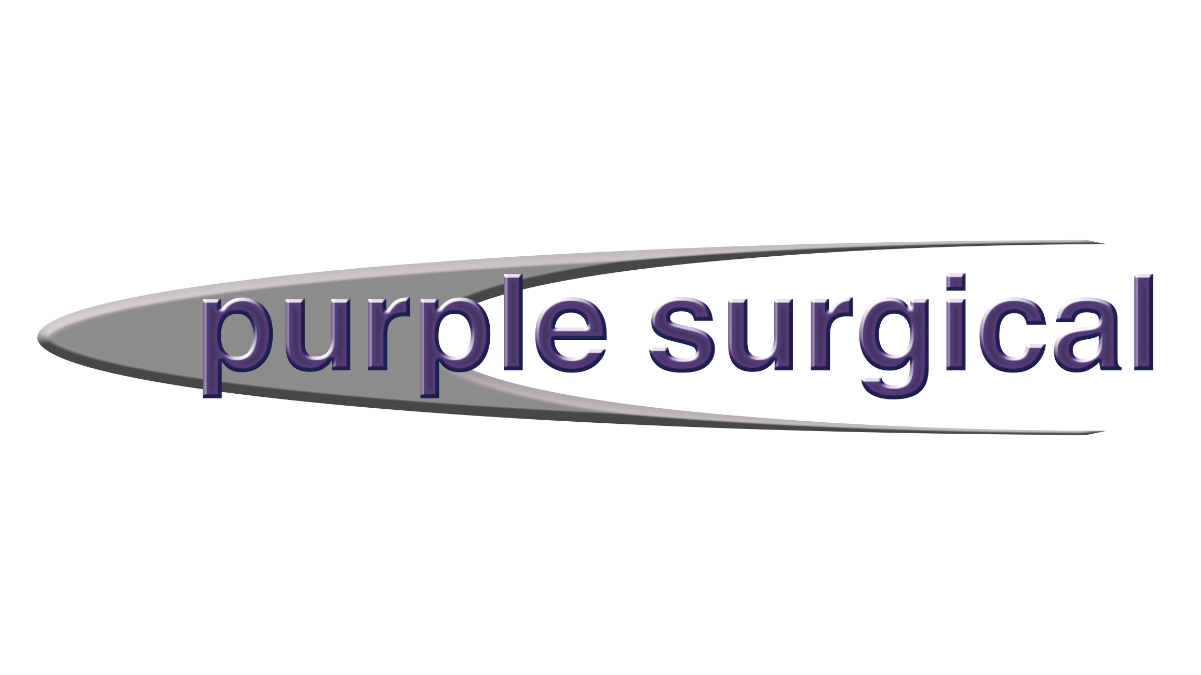

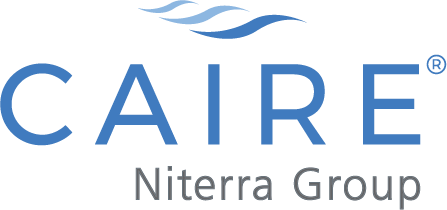
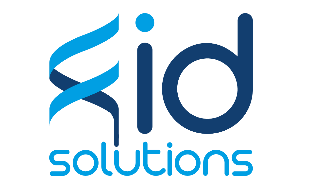
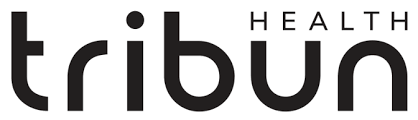
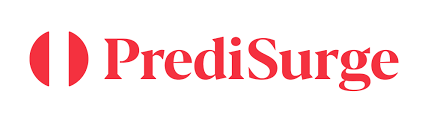
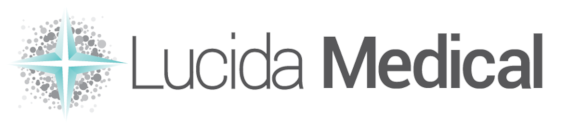
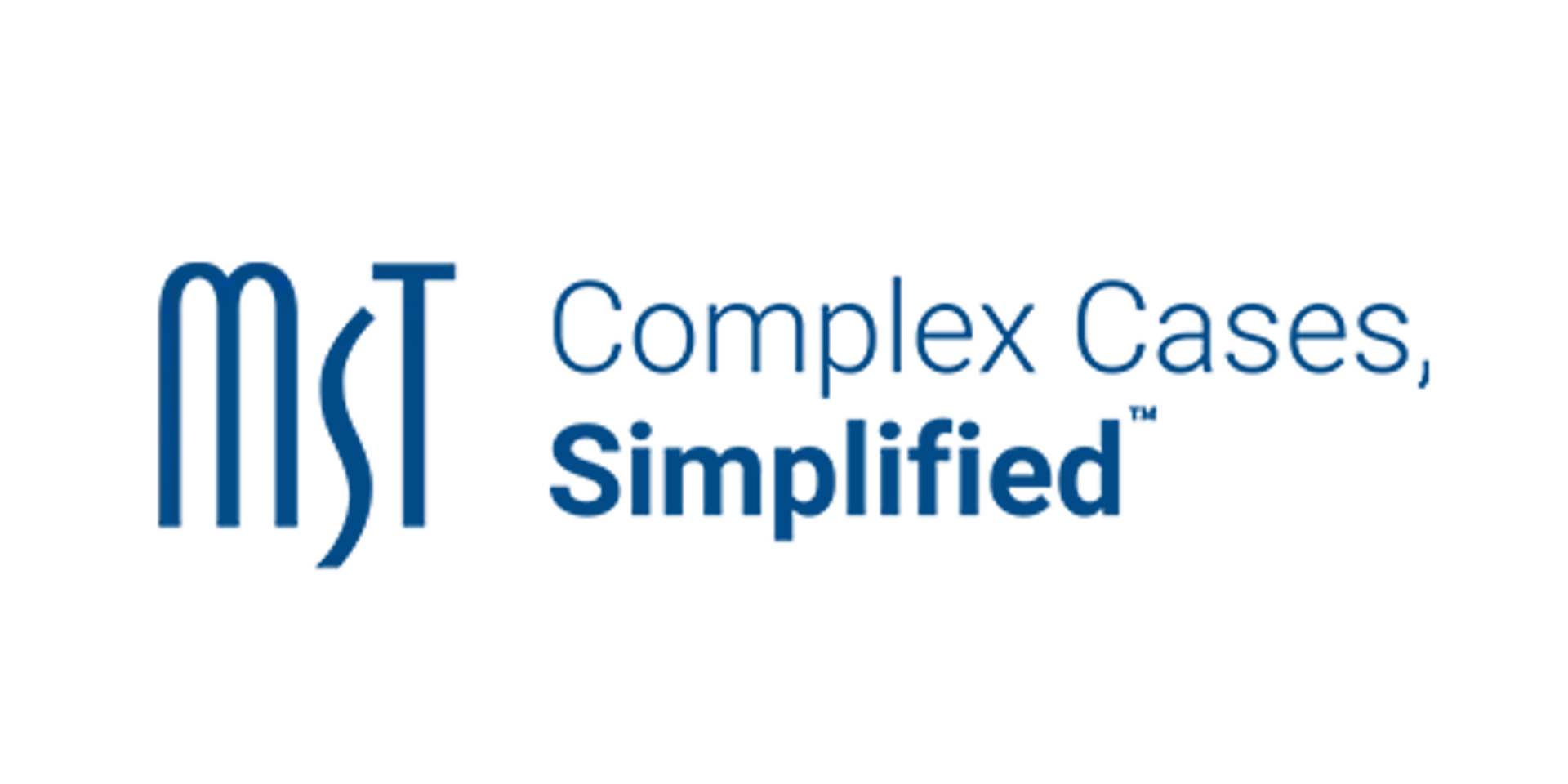
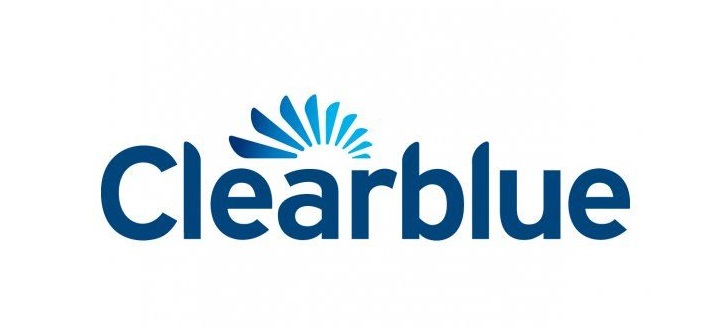
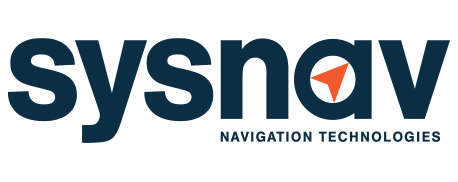
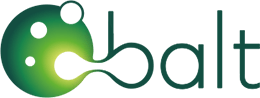
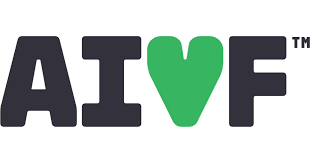
Featured case studies
Streamlining ISO 13485 Certification for a connected medical device
Streamlining ISO 13485 Certification for a connected medical device Introduction Our client is a startup at the forefront of connected health technology (diabetes) Types Quality Management System Implementation, ISO 13485 Certification Scope of work Apotech’s comprehensive support included a preliminary gap analysis, development and implementation of quality management systems tailored to the unique needs of…
Prosthesis manufacturer
Prosthesis manufacturer Introduction As part of their international development strategy, our client wanted to get MDSAP certified with a focus on Canada, Australia and Brazil. They were MDSAP certified within 7 months. Types MDSAP Audit Preparation, Quality Management System Review Scope of work Selecting the certification body (quotes, Q&A) Review of their quality management system…