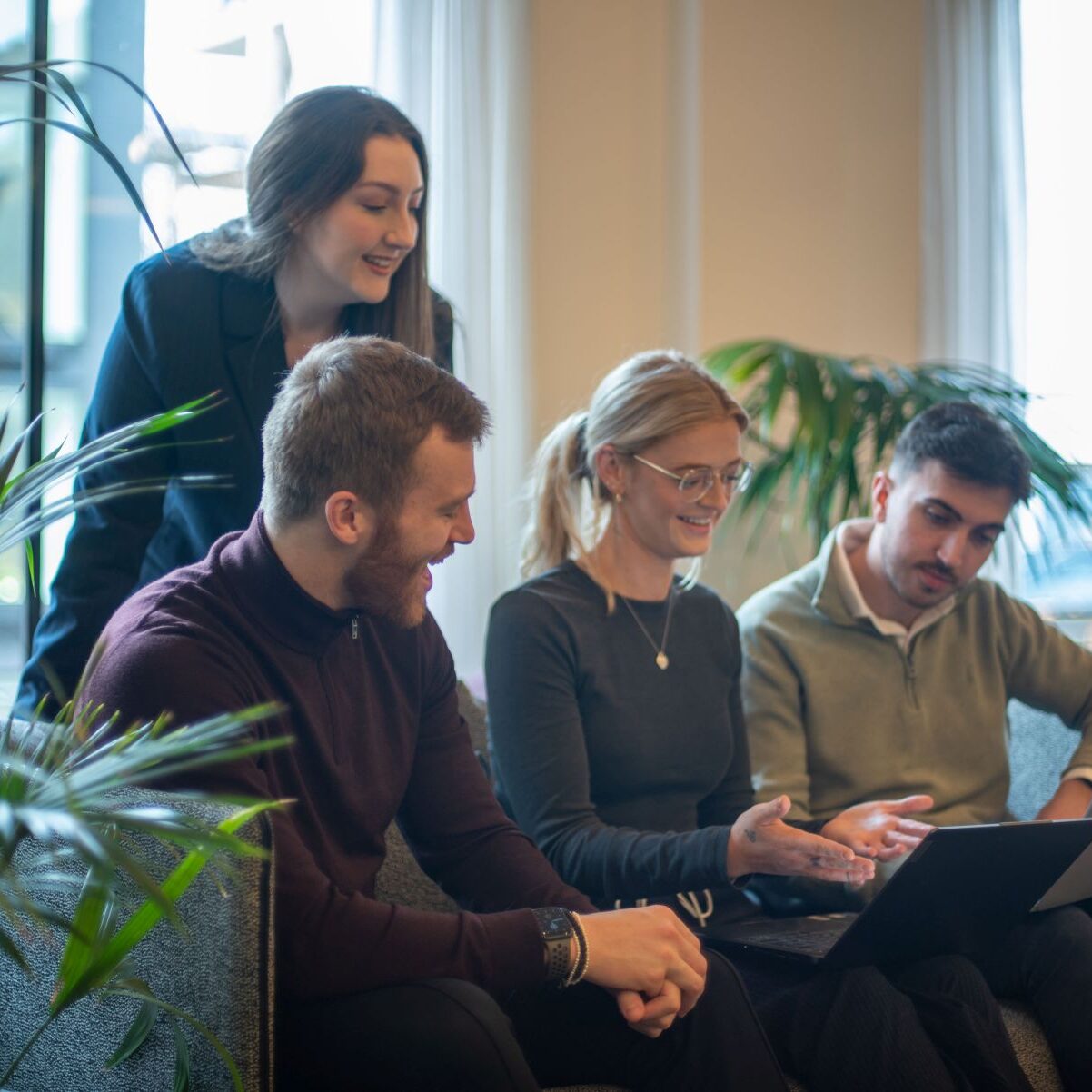
Quality Systems and Compliance
From start-ups to larger global organisations, our experienced team at Apotech helps MedTech companies of all shapes and sizes improve the quality and compliance of their products.
Practical solutions designed to deliver results
Adopt a risk-based approach to improve your quality and compliance.
At Apotech, our experienced consultants can help you improve the quality and compliance of your MedTech products. By taking a risk-based approach, we can help design and implement practical solutions that are proven to deliver results.
Adopting this scalable approach is also what allows us to work effectively with a wide range of companies – from research and development-stage start-ups to small and medium enterprises and much larger global organisations.
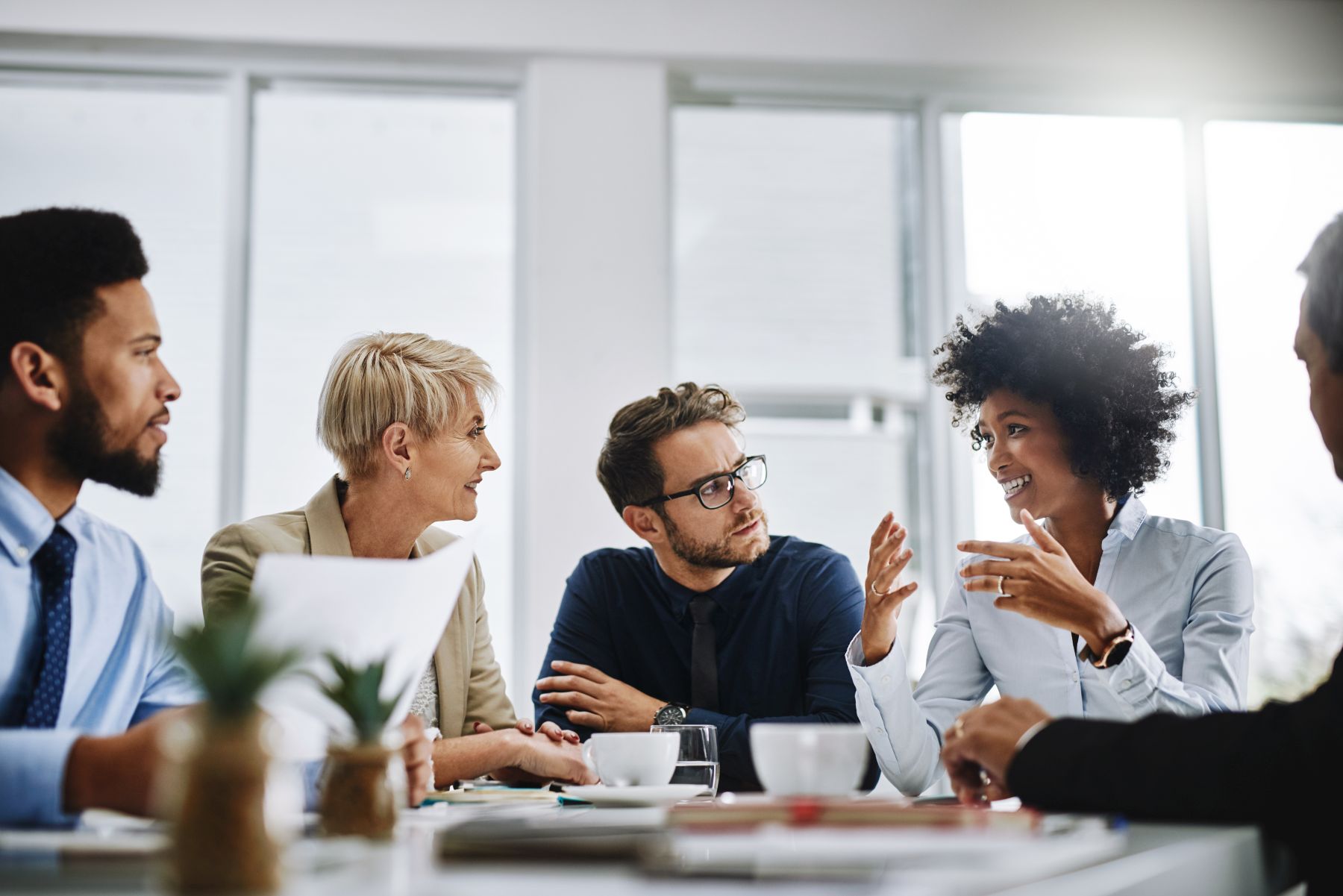
Trusted by top-tier teams worldwide
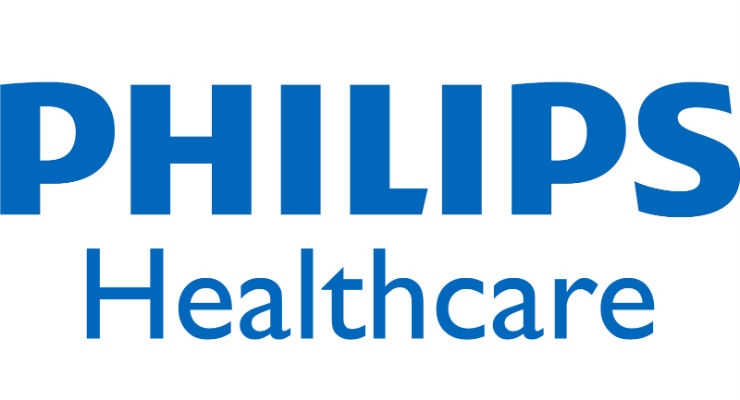
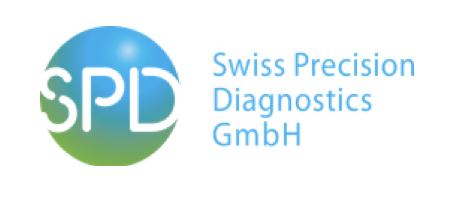
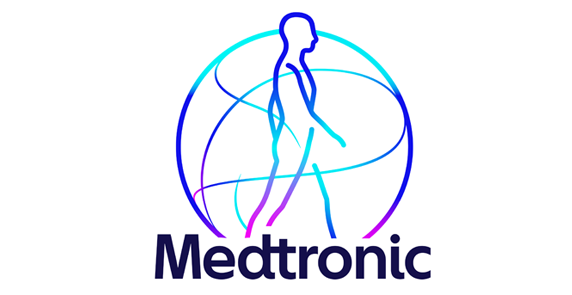
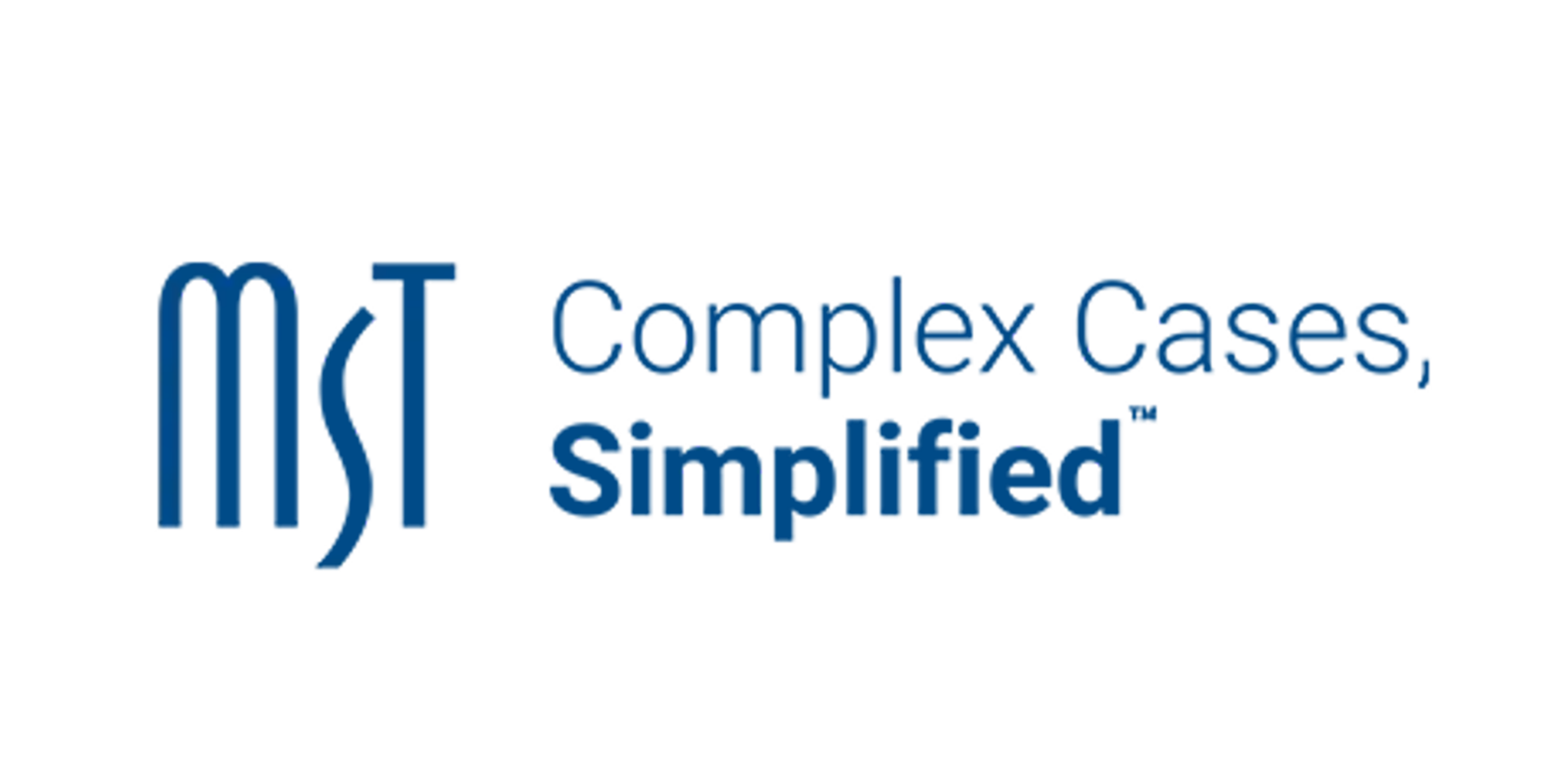
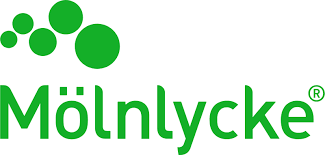
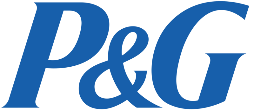
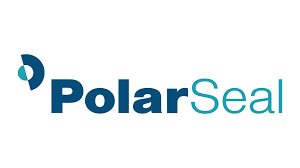
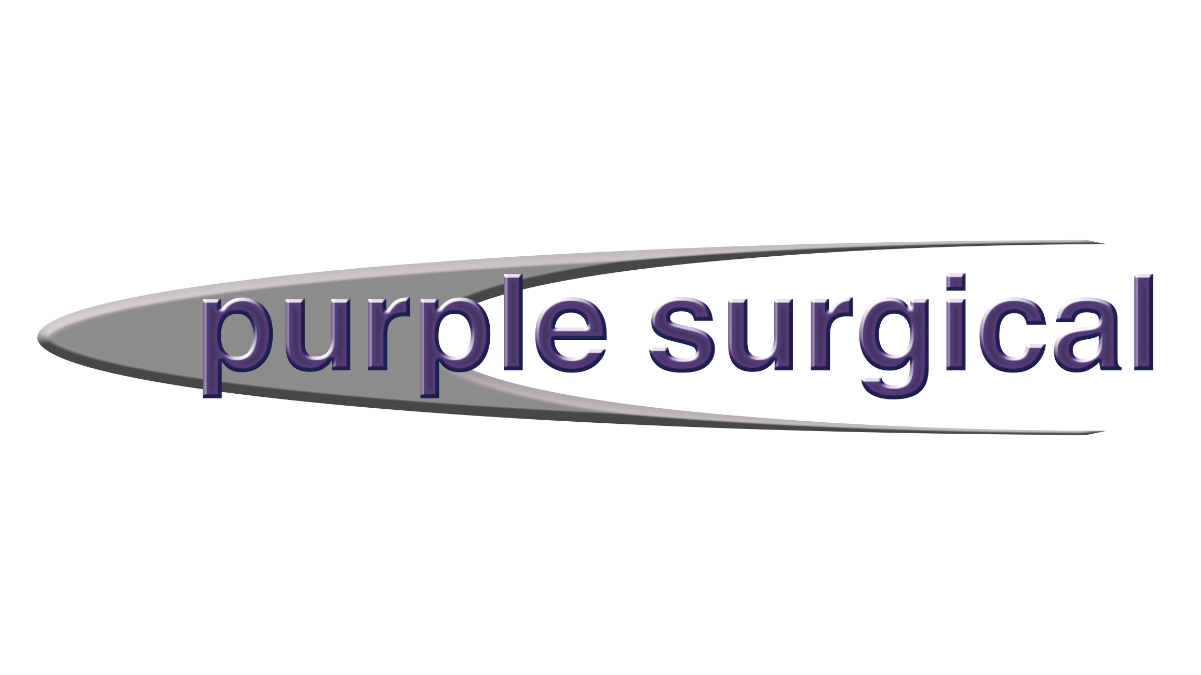

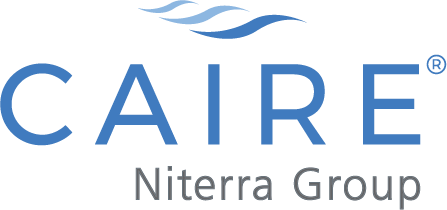
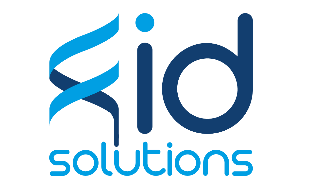
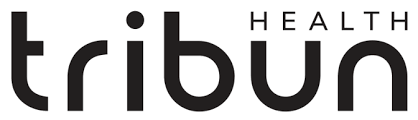
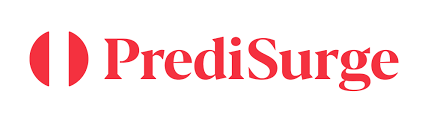
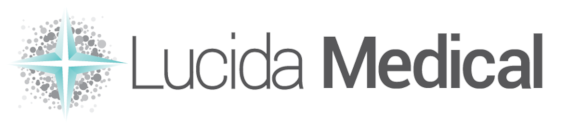
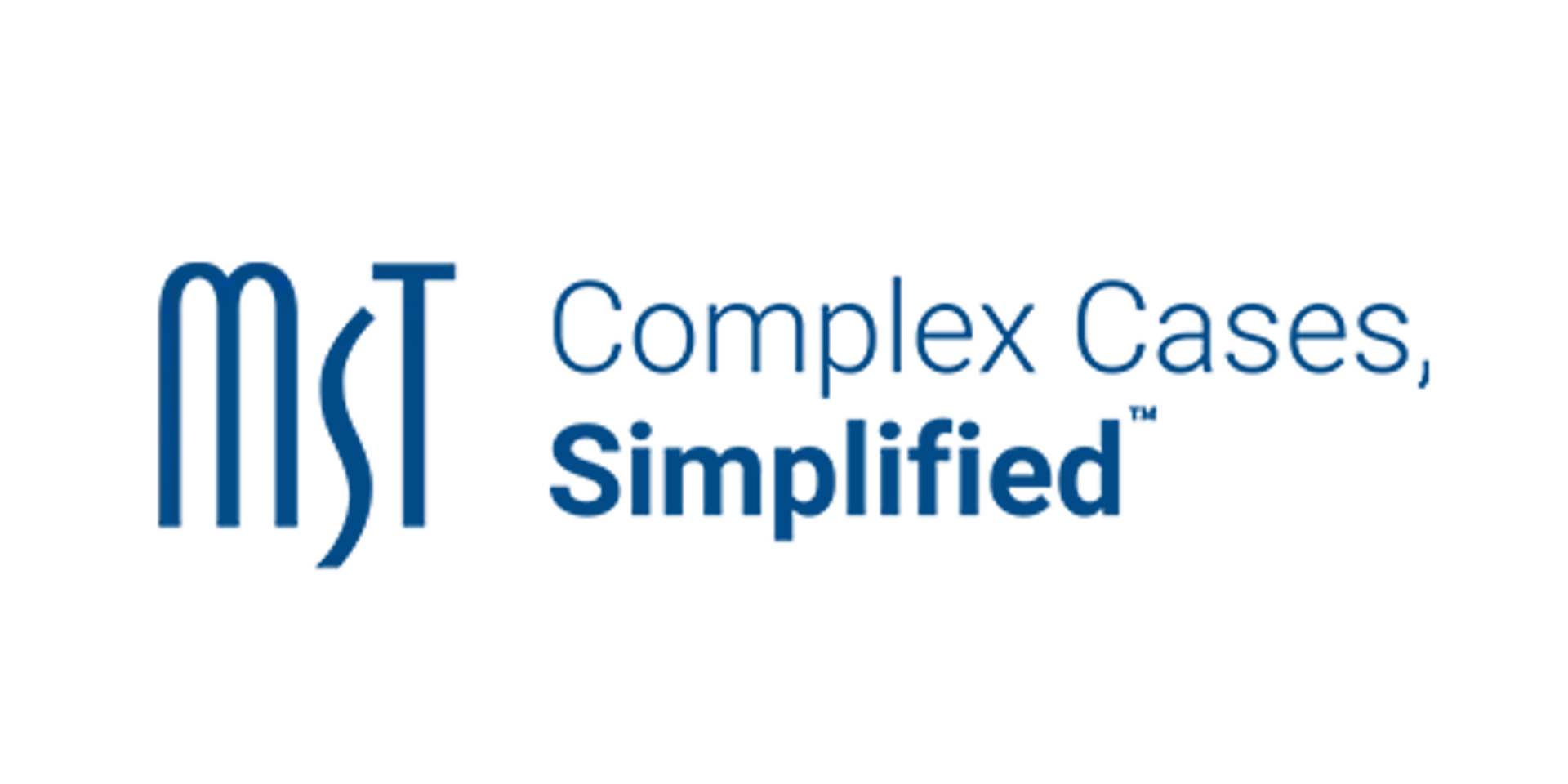
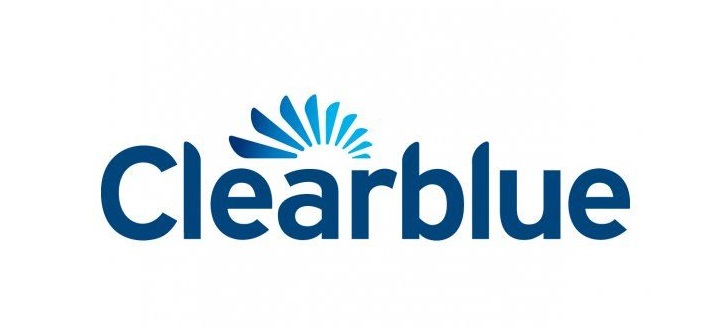
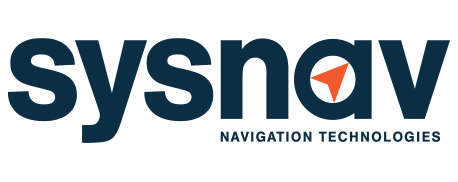
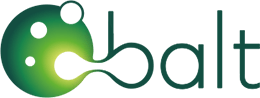
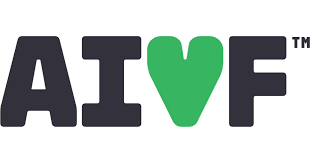
Why choose Apotech’s quality systems and compliance services?
Whether you need help in developing or maintaining your ISO 13485:2016, MDSAP or FDA CFR QSR / QMSR, we can help.
Thanks to our consultants’ in-house experience, we have all the training and expertise required to provide you with a high level of regulatory support and guidance, allowing you to enter into new markets with complete confidence.
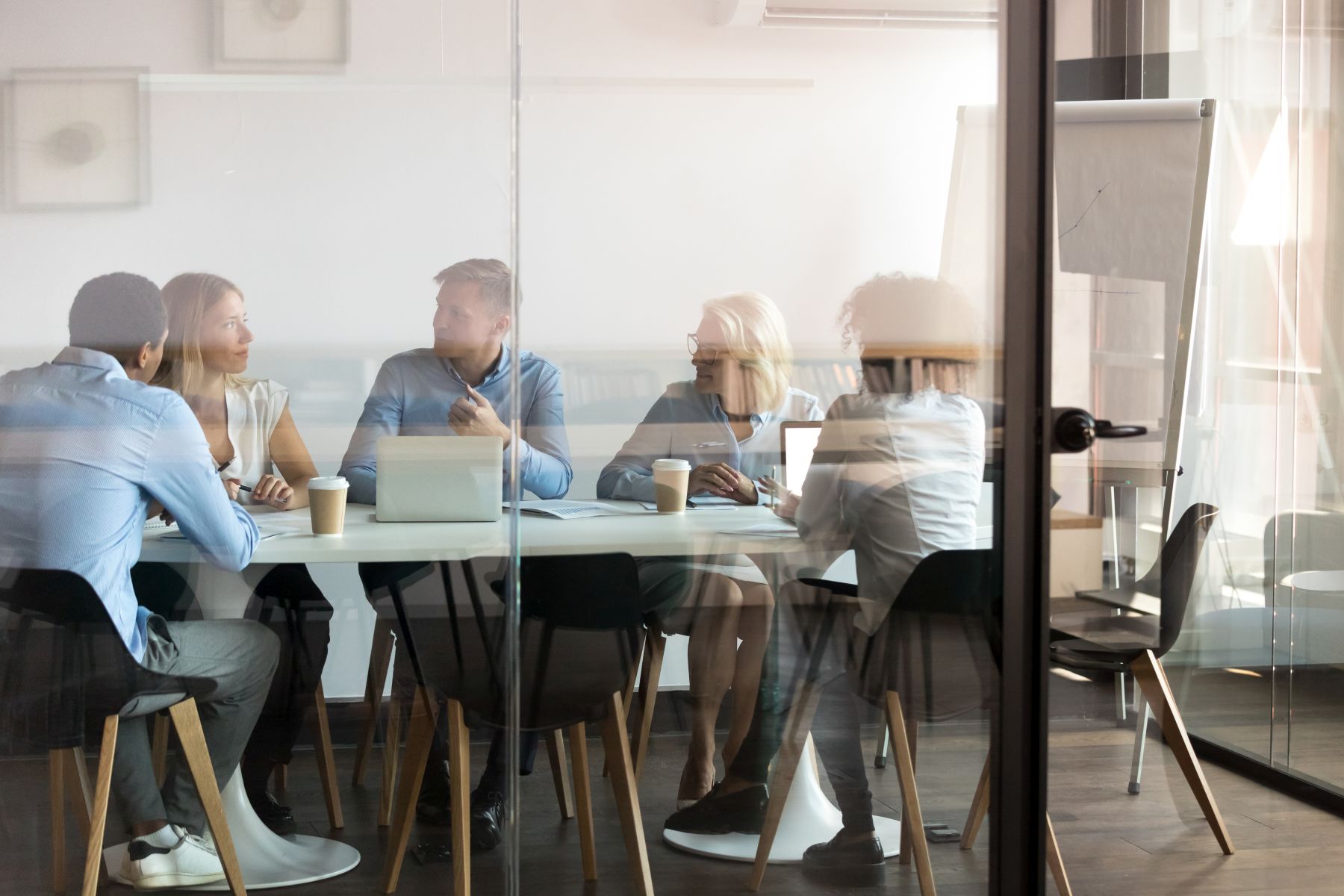
Our range of quality systems and compliance services
At Apotech, our experienced consultants are ready to support you in all of your service needs.
We can help you not only establish and enhance robust quality management systems but we can also conduct thorough audits to guarantee the safety and efficacy of your medical devices.
FAQs on quality systems and compliance
We recognise that the world of quality systems and compliance can be fairly confusing at times. That’s why we aim to make the process as easy to understand as possible by being completely transparent about our services.
Here are some of the questions we are asked most often.
ISO 13485 was introduced in 1996, which happens to be the last time a major update to 21 CFR Part 820 (QSR) occurred. Since that time, ISO 13485 has been modified a few times, and the most recent version – ISO 13485 – is very similar to FDA QSR.
The FDA says it is now time to harmonise the two by replacing the QSR with the QMSR. The primary change here is that Subpart A of the new proposed QMSR refers to ISO 13485 as the basis for compliance with the QMSR but with some minor modifications as discussed below.
This means that all companies required to comply with the QMSR will essentially be following ISO 13485 even if not certified by a third party. Where differences exist between ISO 13485, the Food, Drug, and Cosmetic Act (FD&C Act) and QMSR, the QMSR will prevail.