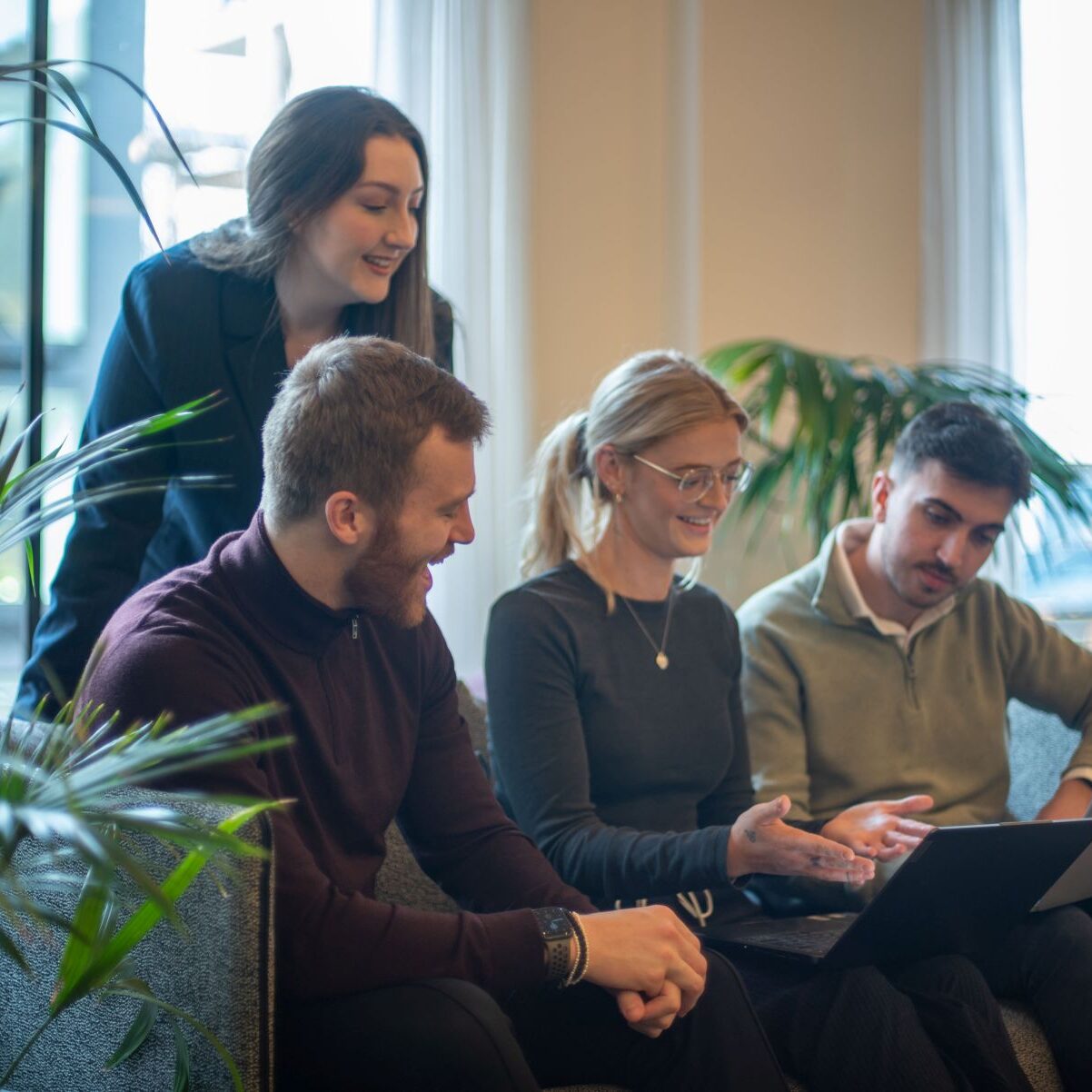
Quality Assurance Services
By partnering with us at Apotech, you will receive unparalleled access to our team’s expertise in quality assurance, allowing you to achieve regulatory compliance all along your product's lifecycle.
Ensuring excellence for the Pharma and Biotech industries
Choose Apotech for tailored, high-level support
At Apotech, we understand the importance of maintaining meticulous quality in all pharmaceutical and biotech processes. From research to manufacturing to distribution, prioritising the quality of your products is imperative to meeting your user needs safely.
That’s why we’ve designed our Quality Assurance services around the unique requirements expected of pharma and biotech companies, allowing you to deliver high levels of quality, compliance and efficiency consistently.
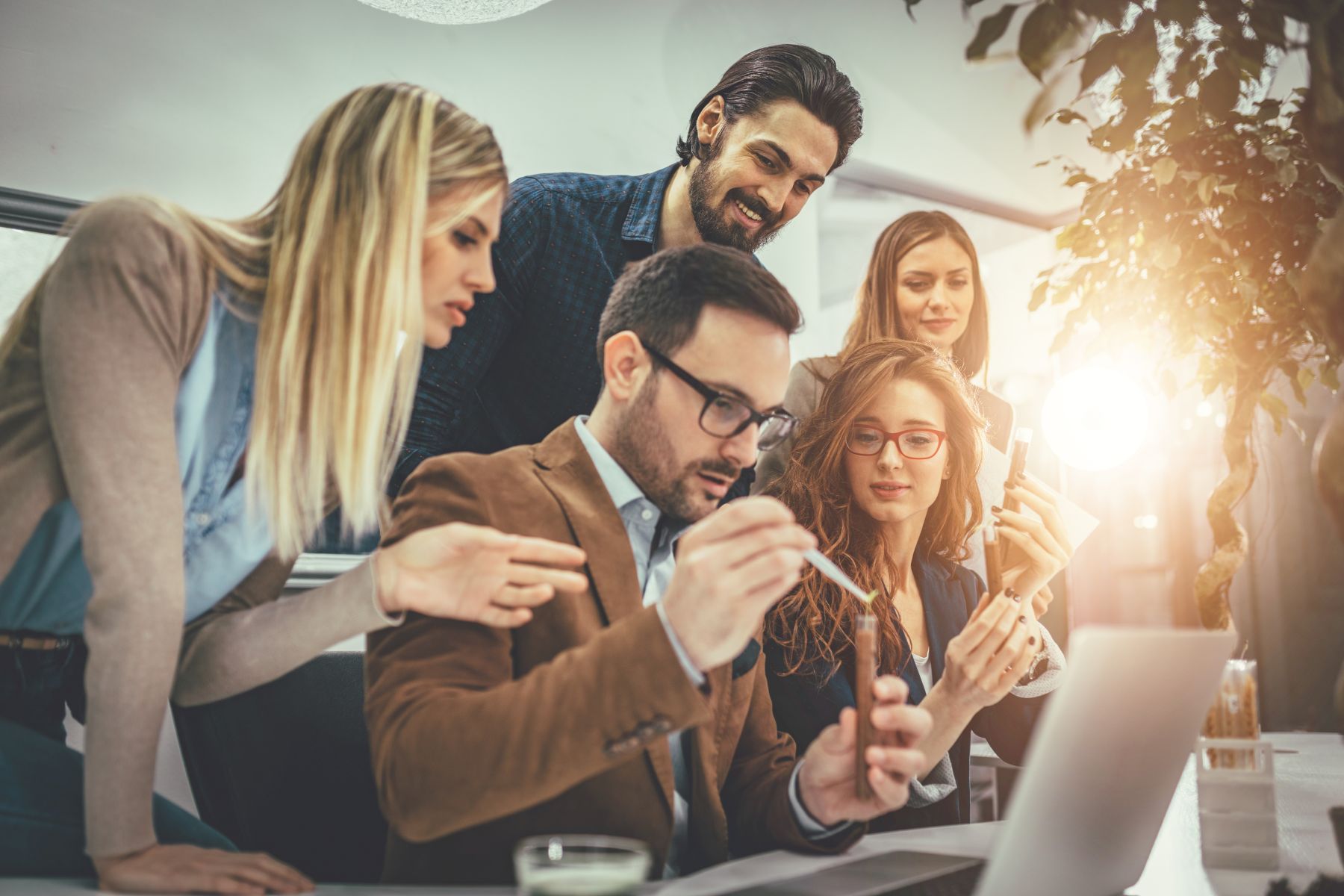
Trusted by top-tier teams worldwide
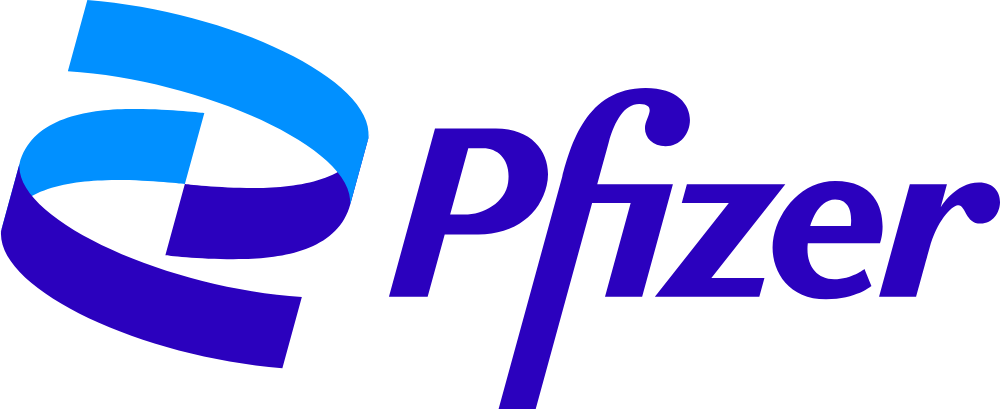
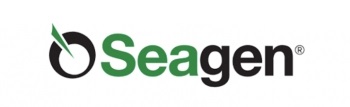
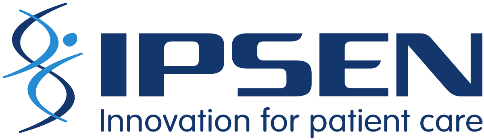
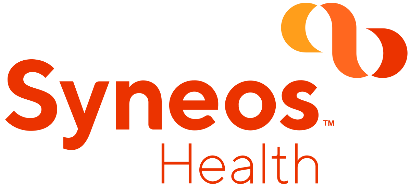
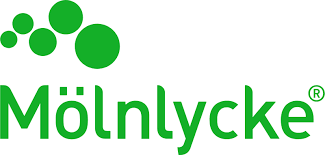
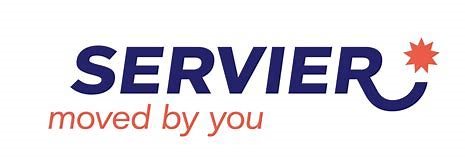
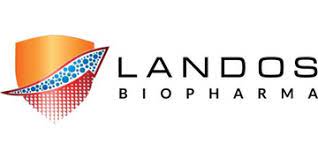
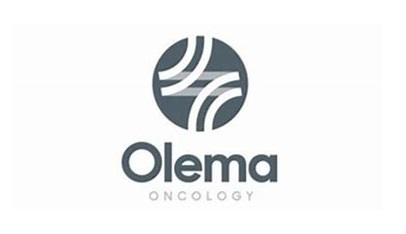
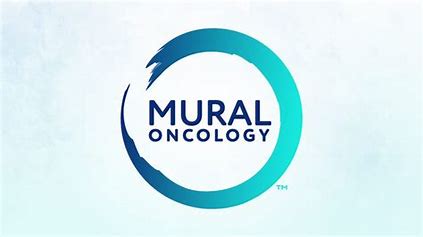
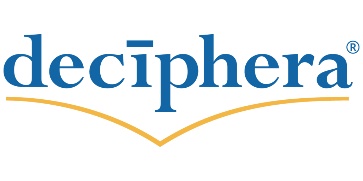
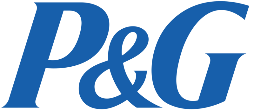

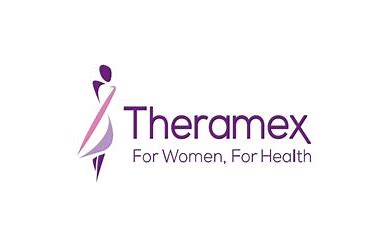
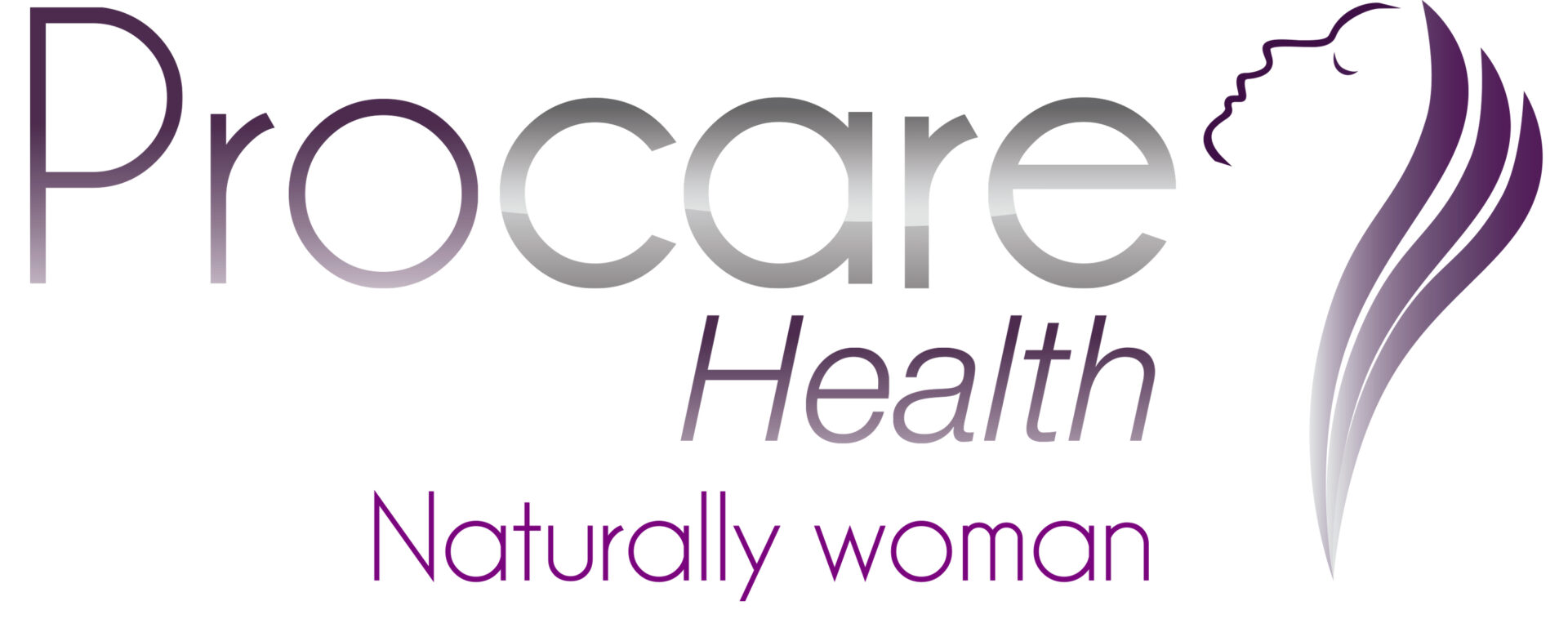
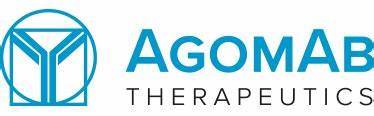
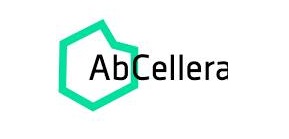
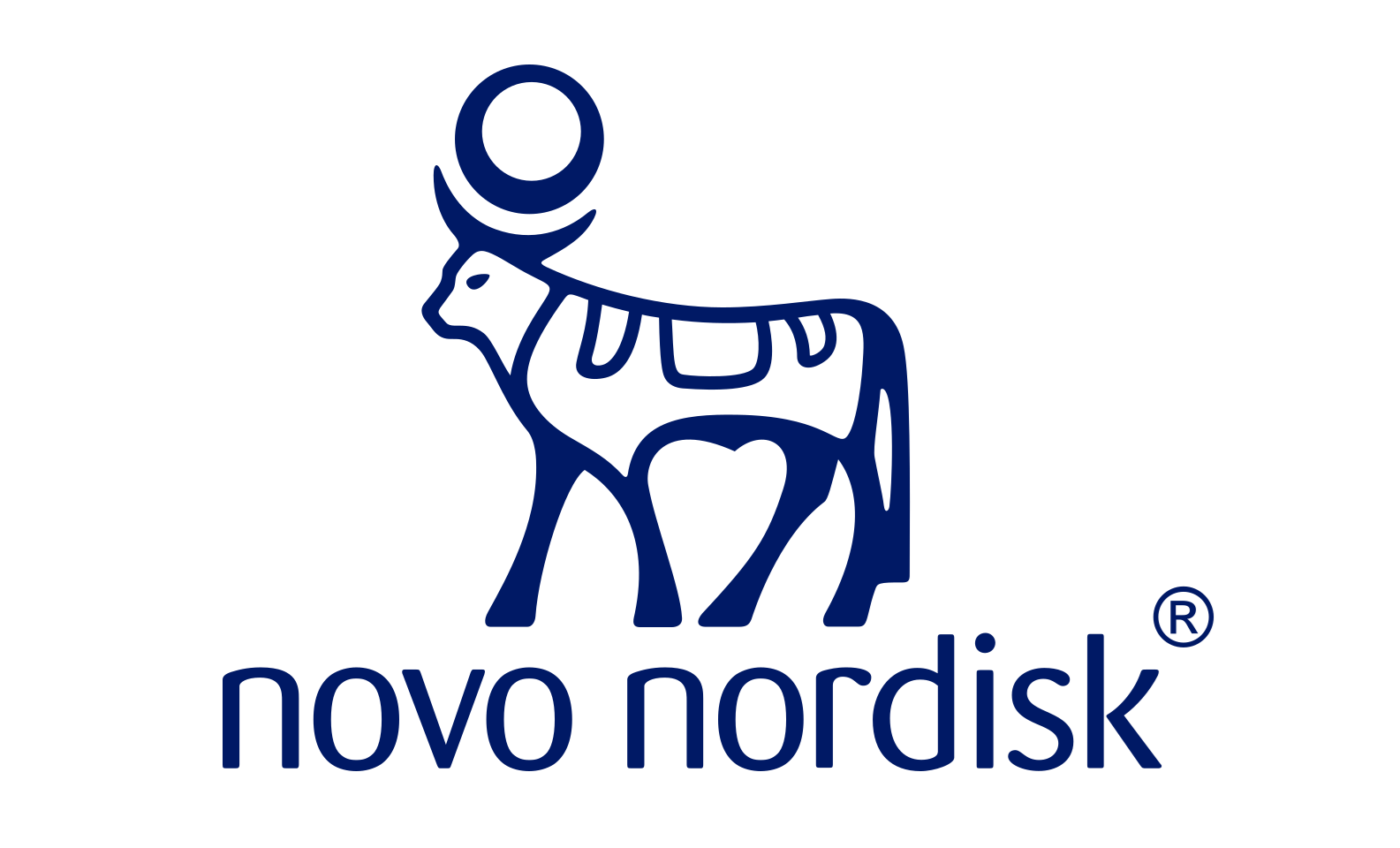
Why choose Apotech’s Quality Assurance services?
Whether you need help establishing your quality management system, conducting a mock inspection, securing a qualified person or implementing a comprehensive training programme, we can help.
With our team’s extensive industry experience, we offer tailored regulatory support and guidance, allowing you to navigate any regulatory requirements with confidence and support at every step.
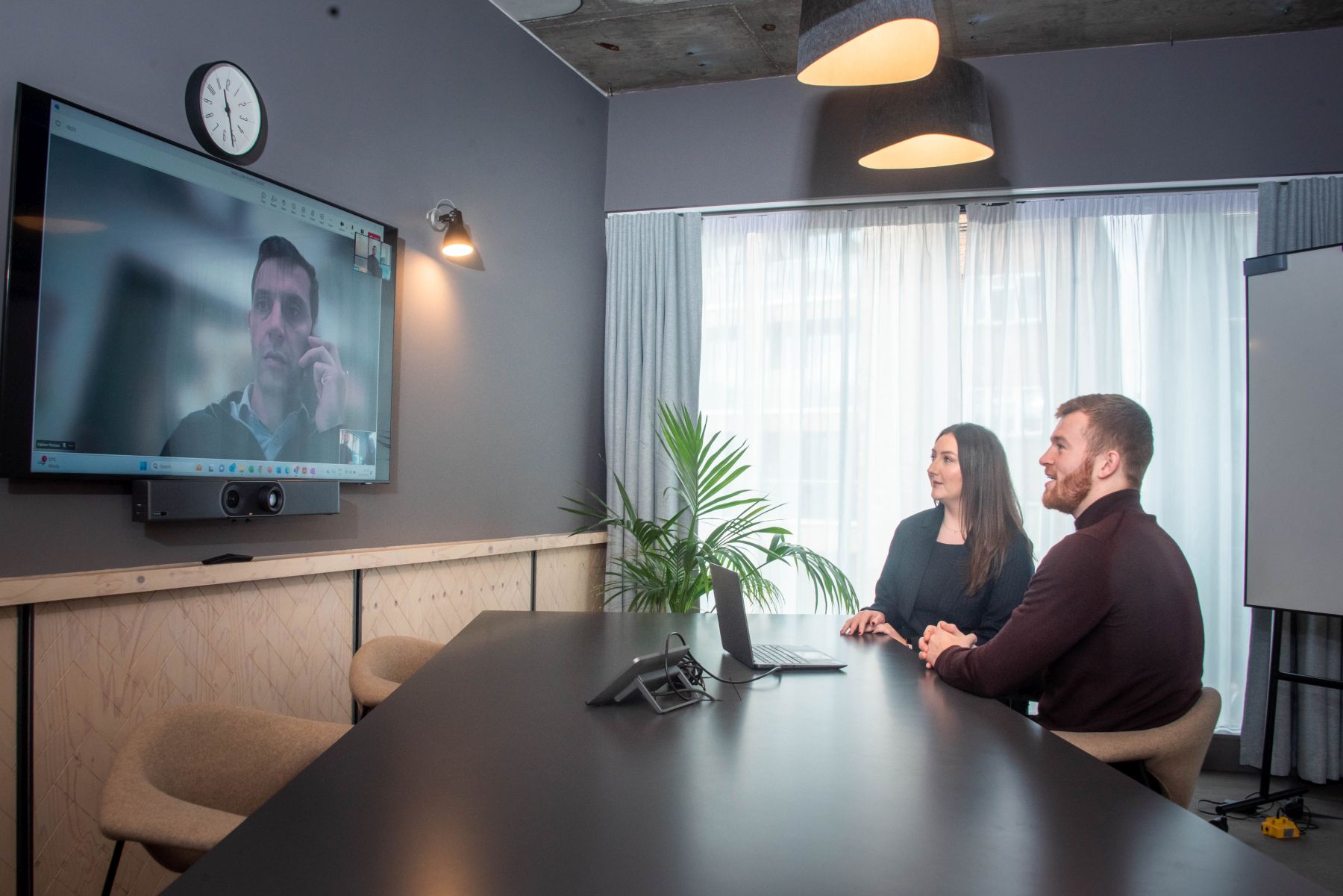
FAQs
At Apotech, we offer full transparency on our Quality Assurance services. We aim to make the process as simple to understand as possible and are always on hand to answer any questions you might have.
Here are some of the questions we get asked most often.
Yes, we have an amazing team of consultants who work with us to perform local activities such as batch release or authoring SOPs in local languages.
As we understand each country's specificities, we can supply you with the right qualified person, according to the local regulations required.
Featured case studies
GMP QA Consulting
GMP QA Consulting Introduction Global API Manufacturer The client was an API manufacturer, with a need for some support to cope with a deviation backlog. Apotech consultant: Two QA Consultants, with backgrounds in sterile devices. Types of Audits GMP Tools: Ishikawa, 5M Audit Locations Europe Scope of work Under the QA director supervision, our consultant…
Batch Release as EU Qualified Person
Batch Release as EU Qualified Person Introduction Our client is a vertically integrated company in chemical synthesis and manufacturing of generic Active Pharmaceutical Ingredients and Drug Products. Standards and references cGMP ISO 9001 GDPR Trackwise, World Excel, power point Scope of work Remote batch certification and release of medicinal products Provide regulatory expertise as…