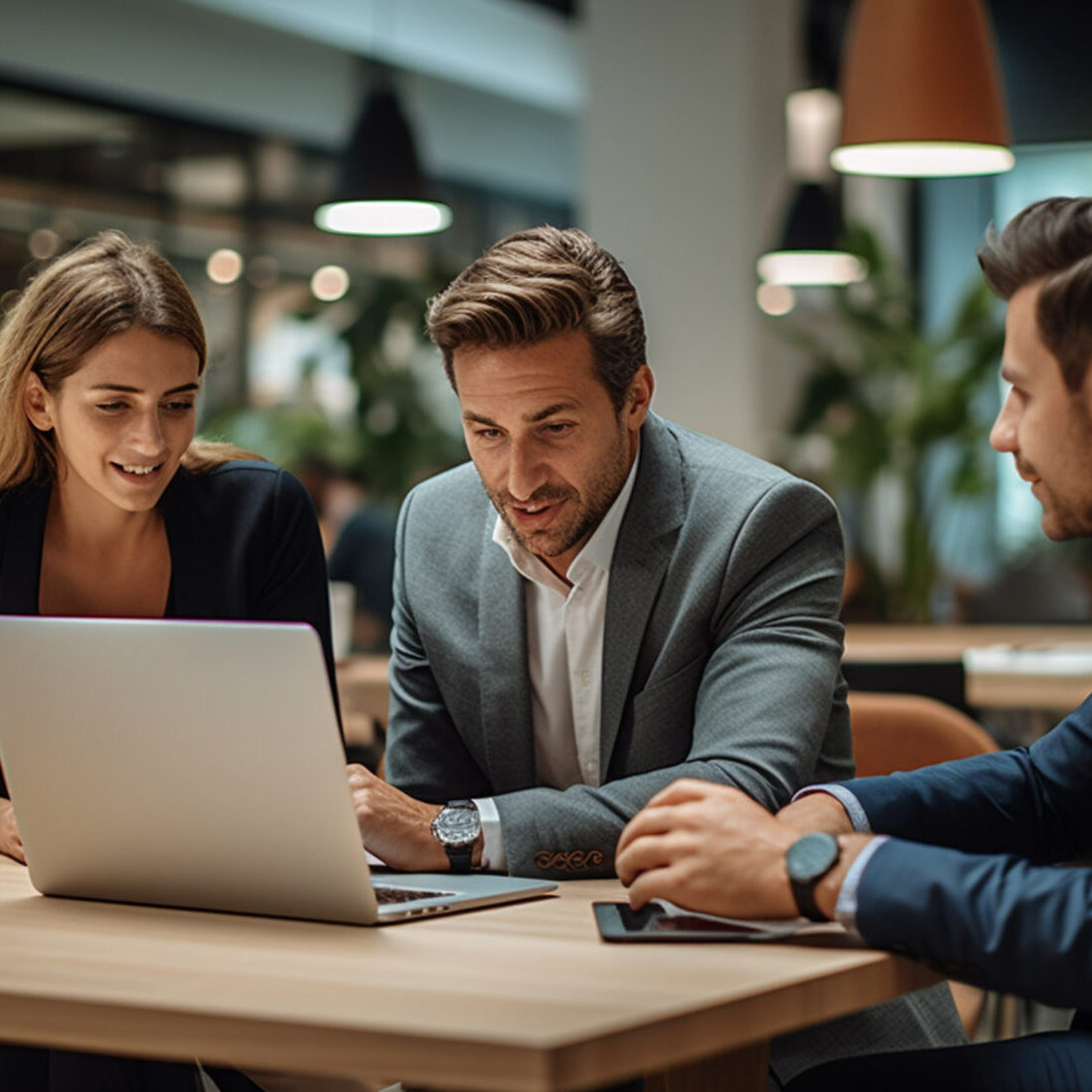
Master your CAPAs : From indentification to implementation
By Imane Nohair, GxP Audit manager at Apotech
The Importance of CAPA in the Pharmaceutical Industry:
The management of Corrective and Preventive Actions (CAPAs) is a fundamental pillar of quality management systems in the pharmaceutical industry. CAPAs play a critical role in preventing the recurrence of non-conformities, ensuring regulatory compliance, and fostering continuous improvement. Effective CAPA management can safeguard public health, streamline operations, and significantly enhance organizational resilience. However, many companies encounter difficulties in implementing CAPAs that are both effective and sustainable due to challenges like inadequate root cause analysis or poor follow-through.
This guide outlines the essential steps to master your CAPA process, from identification to execution, ensuring your organization meets both its regulatory and operational goals.
1. What Exactly Is a CAPA ?
CAPAs can be categorised into two main types. Corrective actions are aimed at addressing the root causes of identified issues, while preventive actions go beyond immediate fixes to avert potential non-conformities in the future. Understanding these distinctions is critical for addressing current problems and proactively mitigating risks.
For example:
π§ Corrective action: Repairing a malfunctioning mechanism that caused a deviation. This action directly resolves the identified issue and prevents its immediate recurrence.
π‘οΈ Preventive action: Establishing a regular preventive maintenance schedule to avoid similar issues from recurring in the future. This step ensures that potential deviations are anticipated and systematically avoided.
2. The necessary steps for an efficient CAPA management:
π Step A: Identifying Non-Conformities
The first step is identifying non-conformities, which can arise from various sources such as internal and external audits, client complaints, production gaps, or regulatory requests. Identifying these issues early can minimize their impact on operations and compliance.
Tools like Electronic Quality Management Systems (eQMS) can aid in centralizing and documenting these non-conformities, providing a clear record of issues and their resolutions.
π Step B: Conducting Root Cause Analysis (RCA)
Conducting a thorough root cause analysis (RCA) is essential for understanding and addressing the underlying reasons behind non-conformities.
Methods such as the “5 Whys,” Ishikawa diagrams, and Pareto analysis help uncover the root causes rather than merely addressing symptoms.
For example: Repeatedly asking “why” can reveal a systemic issue, such as inadequate training, rather than attributing errors to individual oversight.
Training teams to use these analytical tools effectively can significantly enhance their applicability and impact.
π Step C: Planning CAPA Actions
The planning phase involves defining Specific, Measurable, Achievable, Realistic, and Time-bound (SMART) actions.
Detailed action plans ensure clarity, while assigning responsibilities fosters accountability. Establishing realistic timelines and milestones facilitates progress tracking and timely implementation.
For example: A well-drafted action plan for addressing a labeling error might include updating SOPs, retraining staff, and scheduling follow-up audits.
π Step D: Implementing CAPAs
Implementation requires prioritizing actions based on their urgency and importance.
Communication is key to ensuring that all relevant teams understand and execute their responsibilities effectively.
For example: Corrective actions addressing critical compliance issues should be expedited, while preventive measures like system upgrades can follow a structured rollout plan.
β
Step E: Follow-Up and Effectiveness Verification
Organizations must regularly assess whether CAPAs have successfully resolved non-conformities without creating new problems.
Conducting periodic audits or reviews ensures long-term effectiveness.
For example: After implementing a CAPA for a recurring labeling issue, subsequent audits should confirm that errors have been reduced or eliminated, validating the sustainability of the solution.
3. Good Practices for Incorporating CAPA into Your Quality System
π§© Integrating CAPAs into a quality system involves digitalising processes through eQMS tools, regularly training teams on CAPA procedures, and standardising practices through well-defined Standard Operating Procedures (SOPs).
π» Digitalisation enhances efficiency and transparency, allowing for better tracking, documentation, and collaboration.
π Continuous training ensures employees are equipped to recognise and address potential issues, fostering a proactive quality culture.
π Standardisation, on the other hand, ensures consistency in CAPA processes across the organisation, making actions more reliable and repeatable.
4. Case Study: Effective CAPA Management
π A pharmaceutical company faced recurring issues with product labeling following an FDA audit.
π§Ύ The audit revealed that inconsistent label formatting led to regulatory non-compliance and customer dissatisfaction.
π‘ To address this, the company implemented a digital system for centralized label management, ensuring that all labels adhered to FDA standards.
π¨βπ« Employees were trained on the updated labeling requirements, and systematic quality controls were established for each production batch.
π These measures led to a 90% reduction in labeling errors and full compliance during the subsequent FDA audit β illustrating the power of a robust CAPA approach.
5. Tools for Simplifying CAPA Management
π§° Various tools can simplify CAPA management.
π» Specialized eQMS platforms such as Veeva Vault, MasterControl, and TrackWise streamline processes by providing centralized documentation and tracking capabilities.
π€ Collaboration tools like Microsoft Teams, Slack, or Asana facilitate real-time CAPA tracking, enabling teams to monitor progress and resolve bottlenecks efficiently.
π Non-compliance databases, meanwhile, allow organizations to identify and address recurring issues promptly, further enhancing operational efficiency.
6. Key Performance Indicators (KPIs) for Evaluating CAPAs
π Organisations can evaluate the effectiveness of CAPAs using metrics such as:
β±οΈ The average time to close CAPAs
π The frequency of non-conformities
π
The percentage of CAPAs completed within deadlines
π The results of post-CAPA audits
π These KPIs provide actionable insights into the performance of the CAPA process, highlighting areas of success and opportunities for improvement.
7. Common Challenges and How to Overcome Them
β οΈ Challenges in CAPA management include:
- A lack of follow-up,
- Insufficient training, and
- Resistance to change.
π³οΈ A lack of follow-up often leads to abandoned initiatives.
π Insufficient training prevents employees from effectively contributing to CAPA processes.
π Resistance to change can hinder the adoption of necessary improvements.
β These challenges can be addressed by:
- Establishing regular checkpoints,
- Effectively communicating the benefits of CAPAs, and
- Integrating CAPAs into individual and team objectives.
π‘ For example: Emphasizing how CAPAs reduce workload and improve compliance can help overcome resistance and foster a culture of proactive quality management.
8. Why Invest in CAPA Management?
πΌ Investing in CAPA management provides numerous advantages, including:
πΈ Reduced costs from non-conformances and recalls
π Enhanced customer satisfaction through consistent quality
π
Better protection of the companyβs reputation and certifications
π‘οΈ Moreover, a well-executed CAPA strategy builds organizational resilience by equipping teams to anticipate and address potential risks effectively.
Conclusion
π§ CAPA management is a strategic approach that ensures compliance and promotes continuous improvement in the pharmaceutical industry.
β By following these steps and leveraging appropriate tools, companies can:
- Effectively address current issues
- Prevent future problems
- Secure long-term success
- Maintain the highest standards of quality and safety